30 - 54 kN (6600 - 11,880 lbf)
Designed for large displacement vibration tests
Ideal for aerospace, automotive and military applications
Product and package testing
Rugged trunnion design
Automatic static and dynamic armature centering
Motorized gearbox for shaker rotation
Usable frequency ranging from 5 to 2500 Hz
Static payload up to 1500 kg (3300 lbs)
Armature displacement up to 100 mm (3.9 in)
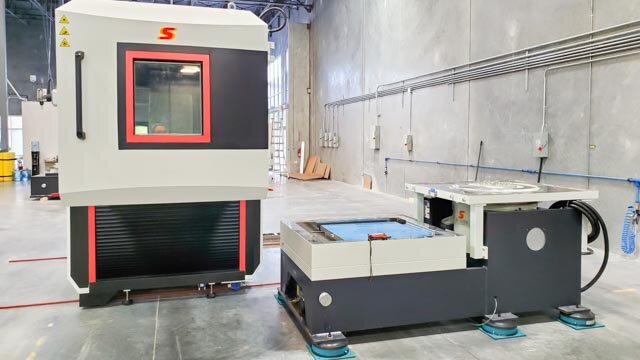
System Performance | T3034A | T4044M | T5444A |
---|---|---|---|
Sine Force Peak kN (lbf) | 29.40 (6600) | 39.20 (8800) | 52.90 (11,880) |
Random Force rms kN (lbf) | 29.40 (6600) | 39.20 (8800) | 52.90 (9,504) |
Shock Force (6 ms) kN (lbf) | 58.80 (13,200) | 78.40 (17,600) | 105.80 (23,760) |
Frequency Range (Hz) | 5 - 2200 | 5 - 2200 | 5 - 2300 |
Continuous Displacement mm (in) | 100 (3.9) | 100 (3.9) | 100 (3.9) |
Shock Displacement mm (in) | 100 (3.9) | 100 (3.9) | 100 (3.9) |
Max Velocity m/s (in/s) | 2.4 (94.4) | 2.4 (94.4) | 2.4 (94.4) |
Max Acceleration Sine Peak m/s2 (g) | 588 (60.0) | 784 (79.9) | 784 (79.9) |
Armature Diameter mm (in) | 445 (17.5) | 445 (17.5) | 445 (17.5) |
Effective Armature Mass kg (lb) | 50 (110) | 50 (110) | 68 (150) |
Max Static Payload kg (lb) | 500 (1100) | 500 (1100) | 800 (2200) |
Common testing standards: MIL-STD-810, MIL-STD 167, ASTM D999-01, ASTM D3580 – 95 (2010), ASTM D4728 – 06, ISO 2247:2000, ISO 8318:2000, ISO 9022-10:1998, ISO 9022-15:1998, ISO 9022-19:1994, IEC 60068-2-64, EIA-RS-186, JIS C 0040:1999 , MIL-STD-202, MIL-STD-750, NAVMAT P-9492, RTCA DO-160 Section 8
POWER AMPLIFIERS
Sentek Dynamics’ PA Series air-cooled, digital switching power amplifiers utilize an intelligent logic control system that assures maximum performance, safety, and reliability. Standard amplifier outputs range from 1 to 480 kVA. Interlocks to prevent shaker damage or operator injury include: Over-voltage, Over-current, Amplifier Over-temperature, Shaker Over-temperature, Over-travel, Phase Failure, and Power-module Fault. The amplifier provides drive power to the shaker, field coils, blower unit and other ancillary components.
High conversion efficiency > 91 percent
Low harmonic distortion < 0.5% at typical testing frequencies
Designed for continuous use over extended periods of operation
LCD display for status and diagnostic messages
Space saving low-profile cabinet for amplifiers with outputs from 1 to 6 kVA
Selectable BNC connection on front panel and rear cabinet for drive input
Meets or exceeds international requirements for safety and EMC
Emergency stop (E-stop) on front panel
Optional remote control panel (RCP) that duplicates functionality of amplifier front panel
VIBRATION CONTROLLER SYSTEM
Unlike traditional vibration test controllers that rely heavily on an external computer for real-time operation, the Spider-81 is the first vibration controller that directly integrates time-synchronized Ethernet connectivity with embedded DSP technology. This strategy greatly increases the control performance, system reliability and failure protection of the vibration test controller. It also allows a large number of channels to be configured without sacrificing system performance.
Mặt trước | Mặt sau |
Random Vibration ControlSpider-81 vibration test controllers have voltage, charge, TEDS, and IEPE inputs which are ideal for shock, vibration and acoustic measurement or general purpose voltage measurement. The internal flash memory stores test configuration data for controlling up to 64 channels simultaneously in addition to storing real-time analysis data. Multiple output channels provide various signal output waveforms that are synchronized with the input sampling rate. A bright LCD screen displays testing status information. Ten monitoring connections on each unit are used to read signals of analog inputs and outputs. Built-in isolated digital I/O and RS-485 serial ports enable interfacing with other hardware.
Swept Sine Vibration Control
Classical Shock Control
Transient Time History (TTH)
Time Waveform Replication
EDM App for iPad
More Vibration Control Software Option
SLIP TABLE
With today’s demanding test requirements there is an increasing need for slip tables to facilitate testing in a horizontal position. Sentek Dynamics offers mono-base and stand-alone slip tables in low and high-pressure designs in standard sizes ranging from 300 mm (12 inches) to 2500 mm (98 inches). Custom sizes are also available including expandable slip tables when a larger mounting area is occasionally required.
In a mono-base configuration the shaker and slip table share a structural steel body that enables rapid conversion between vertical and horizontal positions, and the accurate alignment of the shaker relative to the slip table when rotated to the horizontal position.
In a stand-alone configuration an independent steel platform supported by leveling feet allows any vertical shaker from Sentek Dynamics or other manufacturer to couple with the slip table assembly.
HEAD EXPANDER
Sentek Dynamics can provide a wide-range of standard head expanders and custom fixtures for applications requiring a larger mounting area, vertical mounting or simultaneous testing of multiple devices under test (DUTs) in sizes up to 1500 mm (60 inches). FEA is used to ensure an optimal design and superior performance. Standard material is Magnesium with Aluminum an affordable option.
Lates (square or round) for low-frequency (less than 350 Hz) testing where a large mounting area is needed at an economical cost. (Note: Recommended for DUTs with a low center of gravity)
Head expanders (square or round) for working frequencies ranging from 350 to 2000 Hz.
Various insert patterns are available